Actualmente existen tres tipos de vidrio plano en el mundo: el trefilado, el método flotado y el calandrado. El vidrio flotado, que representa más del 90 % de la producción total de vidrio en la actualidad, es el material de construcción básico en el vidrio arquitectónico mundial. El proceso de producción de vidrio flotado se fundó en 1952 y estableció el estándar mundial para la producción de vidrio de alta calidad. El proceso de flotado consta de cinco pasos principales:
● ingredientes
● fusión
● Formación y recubrimiento
● recocido
● corte y embalaje
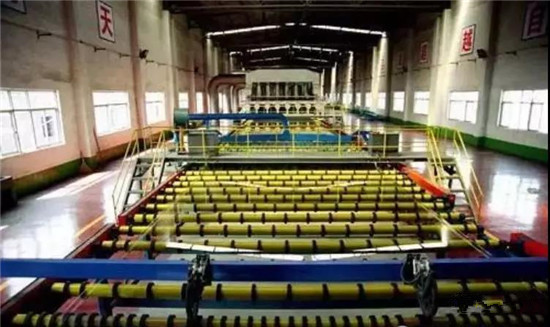
Ingredientes
La dosificación es la primera etapa que prepara las materias primas para la fundición. Entre las materias primas se incluyen arena, dolomita, caliza, carbonato sódico y mirabilita, que se transportan por camión o tren. Estas materias primas se almacenan en la sala de dosificación. La sala de materiales cuenta con silos, tolvas, cintas transportadoras, tolvas, colectores de polvo y los sistemas de control necesarios para el transporte y la mezcla de las materias primas. Desde el momento en que las materias primas llegan a la sala de materiales, se encuentran en constante movimiento.
Dentro de la sala de dosificación, una cinta transportadora larga y plana transporta continuamente las materias primas desde los silos hasta el elevador de cangilones, capa por capa, y luego las envía a la báscula para verificar su peso. A estos ingredientes se añaden fragmentos de vidrio reciclado o devoluciones de la línea de producción. Cada lote contiene entre un 10 % y un 30 % de vidrio roto. Los materiales secos se introducen en la mezcladora y se mezclan. El lote mezclado se envía desde la sala de dosificación al silo del cabezal del horno para su almacenamiento a través de la cinta transportadora, y luego se introduce en el horno a un ritmo controlado mediante el alimentador.

Composición típica del vidrio
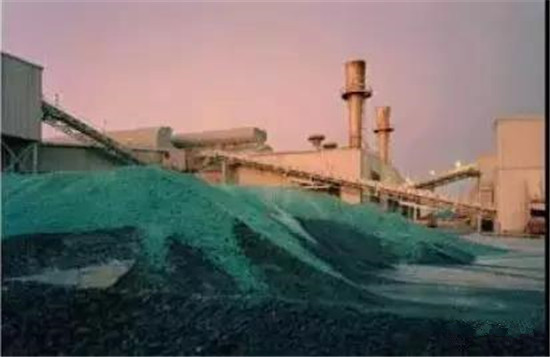
Patio de Cullet
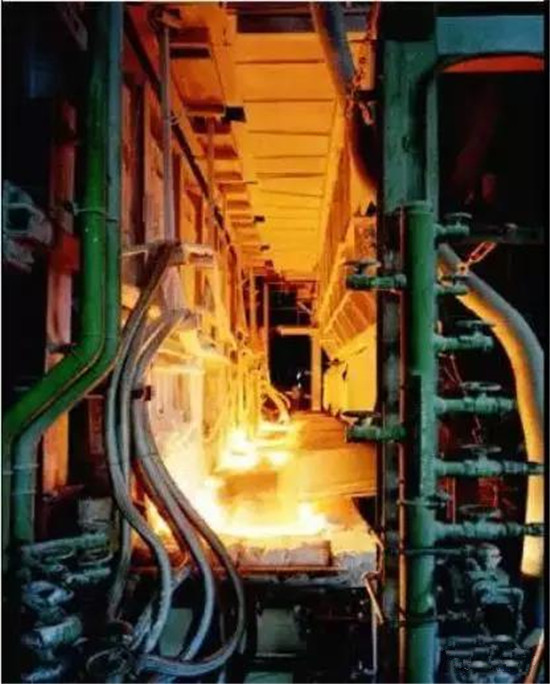
Introduzca las materias primas mixtas en la entrada del horno hasta 1650 grados con una tolva.
Fusión
Un horno típico es un horno de llama transversal con seis regeneradores, de aproximadamente 25 y 62 metros de ancho, con una capacidad de producción diaria de 500 toneladas. Sus componentes principales son la piscina de fusión/clarificador, la piscina de trabajo, el regenerador y un horno pequeño. Como se muestra en la Figura 4, está fabricado con materiales refractarios especiales y cuenta con una estructura de acero en el marco exterior. El lote se envía a la piscina de fusión del horno mediante el alimentador, donde la piscina se calienta a 1650 °C mediante una pistola de pulverización de gas natural.
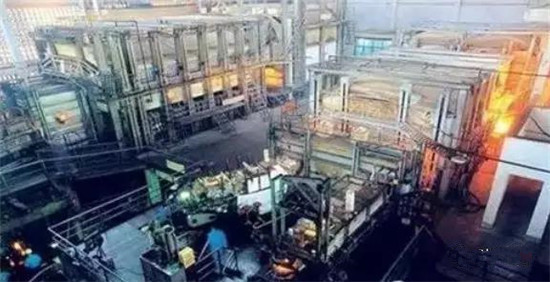
El vidrio fundido fluye desde el baño de fusión hasta la zona del cuello a través del clarificador y se agita uniformemente. Luego, fluye hacia la parte de trabajo y se enfría lentamente hasta alcanzar aproximadamente 1100 grados para alcanzar la viscosidad adecuada antes de llegar al baño de estaño.
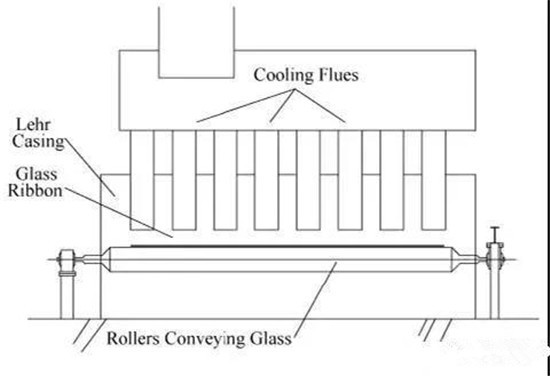
Formación y recubrimiento
El proceso de transformación del vidrio líquido clarificado en una placa de vidrio se basa en la manipulación mecánica, adaptada a la estructura natural del material, cuyo espesor natural es de 6,88 mm. El vidrio líquido sale del horno a través del canal, y su flujo se controla mediante una compuerta ajustable, llamada pistón, que se encuentra a aproximadamente ± 0,15 mm de profundidad en el vidrio líquido. Flota sobre estaño fundido, de ahí el nombre de vidrio flotado. El vidrio y el estaño no reaccionan entre sí y pueden separarse; su resistencia mutua en forma molecular hace que el vidrio sea más liso.
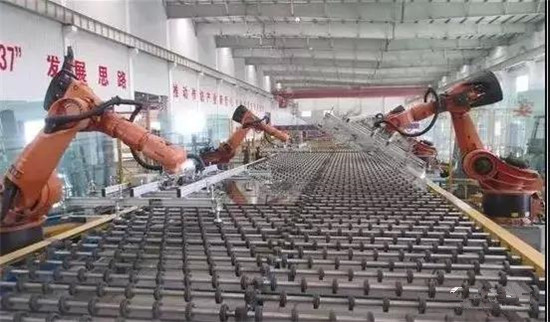
El baño es una unidad sellada en una atmósfera controlada de nitrógeno e hidrógeno. Incluye acero de soporte, carcasas superior e inferior, refractarios, estaño y elementos calefactores, atmósfera reductora, sensores de temperatura, sistema de control de procesos por computadora, de aproximadamente 8 metros de ancho y 60 metros de largo, y la velocidad de la línea de producción puede alcanzar los 25 metros/min. El baño de estaño contiene casi 200 toneladas de estaño puro, con una temperatura promedio de 800 ℃. Cuando el vidrio forma una capa delgada en el extremo de la entrada del baño de estaño, se denomina placa de vidrio, y una serie de extractores de bordes ajustables operan en ambos lados. El operador utiliza el programa de control para ajustar la velocidad del horno de recocido y la máquina de estirado de bordes. El espesor de la placa de vidrio puede estar entre 0,55 y 25 mm. El elemento calefactor de la partición superior se utiliza para controlar la temperatura del vidrio. A medida que la placa de vidrio fluye continuamente a través del baño de estaño, la temperatura de la placa de vidrio disminuirá gradualmente, haciendo que el vidrio sea plano y paralelo. En este punto, se puede utilizar acuracoat® para el recubrimiento en línea de películas reflectantes, películas de baja emisividad, películas de control solar, películas fotovoltaicas y películas autolimpiables en equipos de CVD por pirólisis. En este momento, el vidrio está listo para enfriarse.
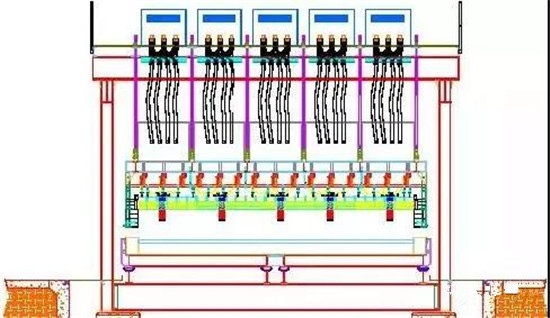
Sección transversal del baño
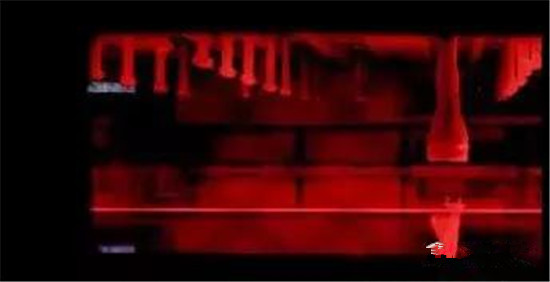
El vidrio se extiende en una capa fina sobre el estaño fundido, se mantiene separado del estaño y se forma una placa.
El elemento calefactor colgante proporciona suministro de calor, y el ancho y el grosor del vidrio se controlan mediante la velocidad y el ángulo del extractor de bordes.
Recocido
Al salir del baño de estaño, el vidrio formado alcanza una temperatura de 600 °C. Si la placa de vidrio se enfría en la atmósfera, su superficie se enfriará más rápido que su interior, lo que provocará una compresión importante de la superficie y una tensión interna perjudicial en la placa.
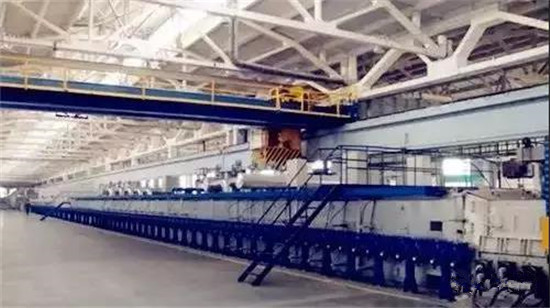
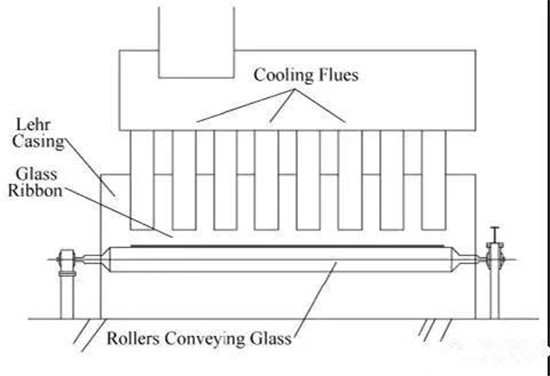
Sección del horno de recocido
El proceso de calentamiento del vidrio antes y después del moldeo también implica la formación de tensiones internas. Por lo tanto, es necesario controlar el calor para reducir gradualmente la temperatura del vidrio a la temperatura ambiente, es decir, el recocido. De hecho, el recocido se lleva a cabo en un horno de recocido con gradiente de temperatura preajustado (véase la Figura 7) de aproximadamente 6 metros de ancho y 120 metros de largo. El horno de recocido incluye elementos calefactores y ventiladores controlados eléctricamente para mantener estable la distribución transversal de la temperatura de las placas de vidrio.
El resultado del proceso de recocido es que el vidrio se enfría cuidadosamente a temperatura ambiente sin tensión ni estrés temporal.
Corte y embalaje
Las placas de vidrio enfriadas por el horno de recocido se transportan a la zona de corte a través de la mesa de rodillos conectada al sistema de accionamiento del horno. El vidrio pasa por el sistema de inspección en línea para eliminar cualquier defecto y se corta con una muela de diamante para eliminar el borde (el material del borde se recicla como vidrio roto). A continuación, se corta al tamaño requerido por el cliente. La superficie del vidrio se rocía con un agente de pulverización para que las placas se puedan apilar y almacenar, evitando que se peguen o rayen. A continuación, las placas de vidrio sin defectos se apilan para su embalaje mediante máquinas manuales o automáticas y se trasladan al almacén para su almacenamiento o envío a los clientes.
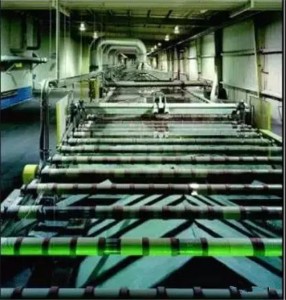
Después de que la placa de vidrio sale del horno de recocido, se forma completamente y se traslada al área de enfriamiento para continuar reduciendo la temperatura.